5S نوعی سیستماتیک از مدیریت بصری است که از همه چیز از نوار کف گرفته تا دفترچه راهنما استفاده می کند. این فقط در مورد پاکیزگی یا سازمان نیست. این همچنین در مورد به حداکثر رساندن بهره وری و سود است. 5S چارچوبی است که بر استفاده از یک طرز فکر و ابزار خاص برای ایجاد کارایی و ارزش تأکید دارد.
این شامل مشاهده ، تجزیه و تحلیل ، همکاری و جستجوی زباله است و همچنین شامل عمل حذف زباله است.
5S شامل پنج اصطلاح است که همه با حرف “S” شروع می شوند.
5S به چه معنی است؟
5S که گاهی اوقات 5s یا Five S نیز خوانده می شود ، به پنج اصطلاح ژاپنی گفته می شود که برای توصیف مراحل سیستم مدیریت بصری 5S استفاده می شود.
هر اصطلاح با S شروع می شود. در ژاپنی ، پنج S عبارتند از Seiri ، Seiton ، Seiso ، Seiketsu و Shitsuke. در انگلیسی ، پنج S به ترتیب مرتب سازی ، تنظیم به ترتیب ، درخشش ، استاندارد سازی و نگهداری ترجمه می شوند.
در 5S پنج روش اصلی وجود دارد. آنها به شرح زیر است:
ژاپنی اصطلاح American Definition
Seiri مرتب سازی بر اساس مواد ، فقط موارد ضروری مورد نیاز برای انجام وظایف را نگهداری کنید. (این عمل شامل مرور تمام محتویات یک فضای کار برای تعیین نیاز و حذف آن است. هر آنچه برای تکمیل روند کار استفاده نمی شود باید منطقه کار را ترک کند.)
Seiton Set in Order اطمینان حاصل کنید که همه موارد مرتب هستند و هر مورد مکانی مشخص دارد. همه موارد باقی مانده در محل کار را به روشی منطقی سازماندهی کنید تا انجام کارها برای کارگران آسان تر شود. این اغلب شامل قرار دادن وسایل در مکان های ارگونومیک است که افراد برای رسیدن به آنها نیازی به خم شدن یا حرکت اضافی ندارند.
Seiso Shine تلاش پیشگیرانه برای تمیز و منظم نگه داشتن محل کار برای اطمینان از کار هدفمند. این به معنای پاکسازی و نگهداری فضای کار تازه سازمان یافته است. این می تواند شامل کارهای معمول مانند غلتیدن ، گردگیری و غیره یا انجام تعمیر و نگهداری در ماشین آلات ، ابزارها و سایر تجهیزات باشد.
Seiketsu Standardize مجموعه ای از استانداردها را برای سازمان و فرایندها ایجاد کنید. در اصل ، این جایی است که شما سه S اول را می گیرید و قوانینی برای نحوه و زمان انجام این وظایف تعیین می کنید. این استانداردها می توانند شامل برنامه ها ، نمودارها ، لیست ها و … باشند
Shitsuke Sustain روشهای جدید را حفظ کنید و برای حفظ نظم و انضباط حسابرسی انجام دهید. این بدان معنی است که چهار S قبلی باید در طول زمان ادامه یابد. این امر با ایجاد احساس نظم و انضباط شخصی در کارکنانی که در 5S شرکت خواهند کرد ، حاصل می شود.
قبل و بعد از اجرای 5S
قبل از 5S
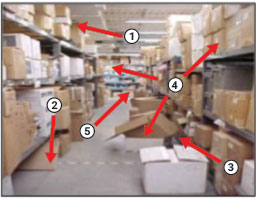
1- موجودی دور از دسترس انباشته شده است
2- موجودی قدیمی استفاده نشده
3- خطر ایمنی جعبه های انباشته شده در راهروها
4- هیچ سازمانی قابل تشخیص مانند بارکد ، قدمت موجودی ، کدگذاری رنگی یا قرارداد نامگذاری وجود ندارد
5- سطل زباله و آوار اجازه جمع شدن دارد
بعد از 5S

1-سطل زباله و دندانه دار کردن یکنواخت
2-ردیابی تاریخ موجودی کالا
3-محتوای سطل آشغال برچسب گذاری شده است
4-سطل های زباله ، قفسه ها و کف ها تمیز و خوب تعمیر می شوند
روشنایی در امکانات کافی است
5-قفسه ها به اندازه کافی کم هستند که برای دسترسی به موجودی کالا از نردبان ها نیازی نیست
5S روش
روش 5S یک رویکرد سیستماتیک برای سازماندهی محل کار است. این روش شامل پنج مرحله مرتب سازی ، تنظیم به ترتیب ، درخشش ، استاندارد سازی و پایداری است.
به طور کلی ، مراحل 5S شامل عبور از وسایل در یک فضای کاری ، حذف موارد غیر ضروری ، سازماندهی موارد ، تمیز کردن ، انجام تعمیر و نگهداری و اطمینان از این است که این موارد به عادت تبدیل می شوند. این مراحل باید به ترتیب انجام شود و باید برنامه ای برای انجام وظایف مرتبط با این مراحل به طور منظم در نظر گرفته شود.
در پایان اجرای 5S موارد مشخصی مانند دفترچه راهنما ، نوار تاریکی یا نوار نور لامپ در کف ، سطل های رنگی ، برچسب های قرمز و پیاده روی 5S مشاهده خواهید کرد. در پایان ، همه اینها باید به کارایی اضافه شود.
روش 5S از ژاپن آغاز شد و اولین بار توسط شرکت موتور تویوتا اجرا شد. این روش به عنوان راهی برای امکان ساخت به موقع (JIT) تولید شده است.
این نوع تولید قصد دارد فقط مقدار محصولی را که لازم است ، در صورت نیاز تولید کند. داشتن یک محل کار سازمان یافته که از نشانه های بصری برای حفظ خود استفاده می کند ، به تولید JIT اجازه می دهد تا روانتر پیش برود. در این نوع محیط ها ، مشاهده مشکلات و جابجایی کارآمد مواد آسان تر است.
منشا 5S
سیستم تولید تویوتا
روش 5S تبار خود را به ژاپن پس از جنگ می رساند ، جایی که رهبران در حال رشد صنایع تویوتا (neé Toyoda Automatic Loom Works) به دنبال کاهش ضایعات تولید و ناکارآمدی بودند. راه حل آنها ، به نام سیستم تولید تویوتا ، شامل چندین روش است که در نوع خود معروف می شوند ، از جمله ساخت Just-In-Time ، Jidoka ، و مفهوم اصلی محل کار بصری.
در ابتدا ، سیستم تولید تویوتا یک راز کاملاً محرمانه بود ، اما رونق گسترده اقتصادی ژاپن که در دهه 1980 تجربه کرد ،
علاقه شدید شرکت های خارجی را جلب کرد که چرا تویوتا ، درخشان ترین جواهر تاج تولید ژاپن ، چگونه توانست بسیاری از محصولات را بسازد ، بنابراین به سرعت ، در چنین سطح کیفیت بالا. با شروع تدریج تبادل نظر بین المللی ، نویسنده و مدیر ULVAC Inc ، هیرویوکی هیرانو ، پنج ستون محل کار بصری را ابداع کرد ، مفهومی که به روش 5S تبدیل می شود ، همانطور که امروزه می شناسیم.
روش 5S در طول سالها اهمیت پیدا کرده است و اکنون یکی از عناصر اساسی Lean است ، همراه با سایر فرایندها و روشهای ناب مانند:
محل کار بصری
شش سیگما
کایزن
کنبان
جمبا
تیموود
تولید ناب